
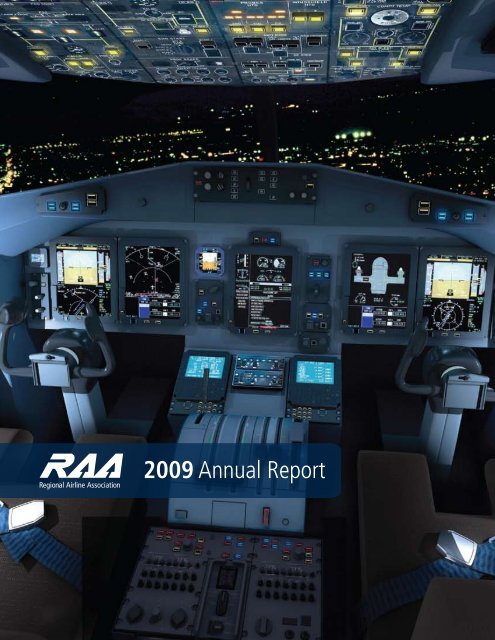

Operational historyīeech sold only eleven Starships in the three years following its certification. įlight instrumentation for the Starship included a 14-tube Proline 4 AMS-850 " glass cockpit" supplied by Rockwell Collins, the first application of an all-glass cockpit in a business aircraft. However, the propellers are operating in a turbulent airflow in the pusher configuration (due to airflow past the wings moving aft in vortex sheets) and high-velocity exhaust gasses are discharged directly into the props, thus the resulting external propeller noise is more choppy and raucous than otherwise would be the case. Mounting the engines so that the propellers are facing rearward, pushing rather than pulling the aircraft, has the potential of a quieter ride since the propellers are further from the passengers and because vortices from the propeller tips do not strike the fuselage sides. In its place, directional stability and control is provided by rudders mounted in the winglets (Beechcraft called them tipsails) at the tips of the wings. Ī traditionally located vertical tail would have transmitted propeller noise into the airframe. As configured, the Starship is difficult to stall-the forward surface stalls before the main lifting surface, which allows the nose to drop and more-normal flight to resume. īeech studied several configurations before settling on a canard configuration in early 1980. Nonetheless, the empty weight of production aircraft exceeded the target by several thousand pounds. According to Beech, the Starship weighs less than it would have if it were built from aluminum.

Beech chose carbon fiber composite for its durability and high strength-to-weight ratio. The Starship is noteworthy for its carbon fiber composite airframe, canard design, lack of centrally located vertical tail, and pusher engine/propeller configuration.Ĭarbon fiber composite was used to varying degrees on military aircraft, but at the time the Starship was certified, no civilian aircraft certified by the US Federal Aviation Administration had ever used it so extensively. The Starship’s unusual design features canards and pusher propellers The first production Starship flew on April 25, 1989. By the end of development, the Starship had grown larger in cabin volume than the King Air 350 while having the same gross ramp weight of 15,010 lb (6,808 kg). The program was delayed several times, at first due to underestimating the developmental complexity and manufacturing learning curve of the production composite construction, and later due to the technical difficulties of correcting a pitch damping problem and developing the stall-warning system. NC-2 was used for avionics and systems testing and NC-3 was used for flight management system and powerplant testing. NC-1 was used for aerodynamic testing and was the only Starship equipped with conventional electro-mechanical avionics. Beech built three airworthy full-scale prototypes. Prototypes were produced even as development work was continuing-a system demanded by the use of composite materials, as the tooling required is very expensive and has to be built for production use from the outset. Only one POC was built and it has since been scrapped. This aircraft had no pressurization system, no certified avionics, and a different airframe design and material specifications than the planned production Model 2000. The POC aircraft first flew in August 1983. One of the significant changes made to the design by Scaled Composites was the addition of variable geometry to the canard. On August 25, 1982, Beech contracted with Scaled Composites to refine the design and build an 85% scale proof-of-concept (POC) aircraft. The design was originated by Beechcraft in January 1980 as Preliminary Design 330 (PD 330). Development of the Starship began in 1979 when Beech decided to explore designs for a successor to its King Air line of turboprops that would fly faster and carry more passengers.
